Cycles with pressure support
Discover how cycles with pressure support enable the sterilization of delicate products while safeguarding their structural integrity and ensuring optimal results. Read the article for more details.
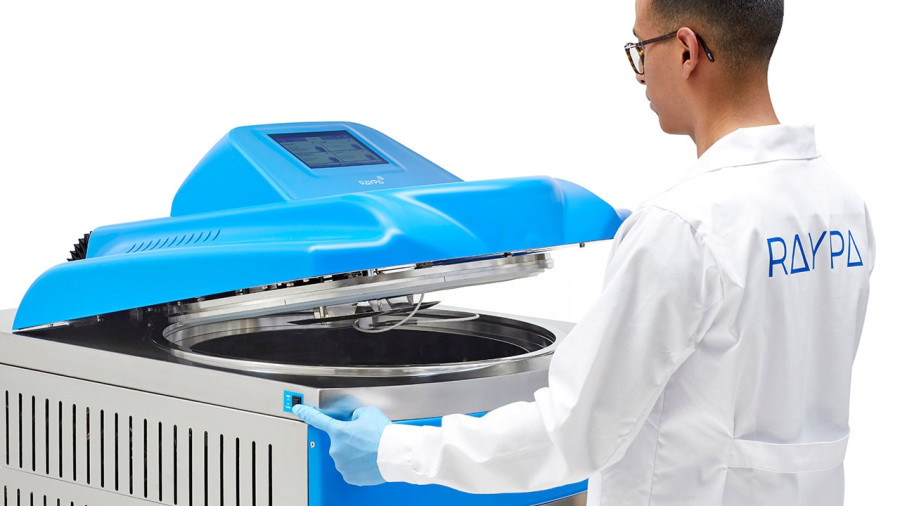
In the field of sterilization technology, the introduction of the cycle with pressure support in autoclaves represents a significant advancement, particularly concerning the sterilization of packaged products such as collyriums, vials, pre-filled syringes, pouches, and canned foods.
Understanding this process begins with recognizing the necessity of controlling the pressure differential between the interior of the packages and the chamber pressure during the sterilization and cooling phases.
To mitigate the risk of excessive pressure differentials, cycles with pressure support have been developed, incorporating the strategic use of compressed air. Through controlled injection of compressed air into the sterilization chamber, these cycles minimize the pressure differential, thereby preserving the structural integrity of the processed containers.
Types of cycles with pressure support
Cycles with pressure support in autoclaves have two main variants: the Air over-pressure cycle and the steam-air-mix cycle. Each variant is designed to meet specific needs and adapt to different types of loads.
Air over-pressure cycle
The air over-pressure cycle, also referred to as air ballast, represents an advanced adaptation of the standard liquids cycle. This technique integrates the use of compressed air with a fast cooling system, specifically designed for the sterilization of semi-open containers. The primary advantage of this method lies in its ability to minimize liquid loss due to evaporation during the cooling phase, making it particularly suitable for contexts where even minimal liquid loss is unacceptable. This cycle is commonly employed for sterilizing items such as preloaded pipettes, vials containing solutions, glassware covered with aluminum foil, and other containers that allow partial ventilation.
As previously discussed in our post on the standard cycle for the sterilization of liquids, it is crucial to perform controlled and gradual depressurization during the cooling phase to prevent sudden boiling of the contents. However, the standard liquid cycle fails to address the issue of liquid mass loss due to evaporation that occurs from the end of the sterilization phase through to the conclusion of the cooling phase. To mitigate this issue, the air over-pressure cycle introduces compressed air into the chamber to maintain pressure, thereby reducing the partial pressure of the vapor. This reduction, in conjunction with accelerated decreasement of the temperature thanks to the fast cooling system, significantly reduces the evaporation of the load, allowing the materials to cool rapidly without substantial liquid mass loss.
Functionally, the air over-pressure cycle bears similarities to the steam-air mix cycle, as both methods pressurize the autoclave chamber using a combination of steam and compressed air. However, while the steam-air mix cycle incorporates air during both the sterilization and cooling phases, the pressurized cycle differentiates itself by injecting compressed air exclusively during the cooling phase.
While the steam-air mix cycle is generally applied in scenarios where sealed containers develop high internal pressure and risk deformation or rupture, the air over-pressure cycle aims to minimize evaporation loss of the liquid load during the cooling phase, offering an optimal solution for the preservation of liquids in semi-open containers.
A clear application example where the air over-pressure cycle is preferable is in the processing of semi-open bottles containing culture media or in the pharmaceutical sector when processing small-volume containers where water loss due to evaporation is unacceptable.
Typically, autoclaves capable of performing cycles with pressure support are also equipped with a fast cooling system, such as an internal fan and an external water-cooled coil surrounding the chamber.
The combination of both systems, accelerating temperature reduction and elevating chamber pressure, prevents load evaporation, enabling a final phase of the cycle with minimal or no liquid mass loss.
Steam-air-mix cycle
As we have discussed, the air over-pressure cycle involves the strategic use of compressed air during the cooling phase to prevent the evaporation of liquids in partially or fully open containers. However, for the sterilization of hermetically sealed objects, a different cycle, known as the steam-air-mix cycle, is required.
The necessity for this cycle arises from the fundamental need to equalize the internal and external pressures of containers to prevent deformation or rupture due to the thermal expansion of its contents when heated to temperatures exceeding 120ºC.
As illustrated in the image, the injection of compressed air into the chamber during the sterilization phase ensures that there is no excessive pressure differential between the internal pressure of the container and that of the chamber.
However, as you may be aware from reading our blog attentively, the introduction of cold air into the chamber acts as a thermal insulator and hinders the access of steam to the surfaces of the load. This is because most of the gases that compose air, such as nitrogen or carbon dioxide, are non-condensable gases.
These gases prevent the steam from condensing on the surface of the load, thereby impeding the heat transfer from the steam to the load, which slows down the heating of the load and reduces the efficacy of the sterilization process. Therefore, any autoclave performing steam-air-mix cycles must be accompanied by a robust homogenization system that ensures an excellent stability and homogeneity of temperature throughout the load throughout the entire duration of the sterilization phase.
These systems employ techniques that mechanically agitate the atmosphere or even the load itself. Examples of such systems include radial fans or agitation systems.
After completing the sterilization phase, similar to the air over-pressure cycle, high pressure is maintained in the chamber to protect the structural integrity of the load while the chamber temperature, and consequently the internal pressure of the processed items, decreases.
As in the air over-pressure cycle, the steam-air-mix cycle is usually accompanied by a fast cooling system. However, a significant difference is that when dealing with hermetically sealed containers, the fast cooling system often employed involves the direct injection of cold water into the chamber. This method is particularly prevalent in the food industry, where cold water immersion via spray showers is used to cool down canned products or pouches following the sterilization phase.
A practical example illustrating the necessity of this type of cycle is the sterilization of pre-filled syringes. During the sterilization phase, without adequate pressure support, reaching 121ºC could cause the liquid inside the syringe to force the plunger outward due to the internal pressure created during this phase. Conversely, during the cooling phase, if the chamber pressure is not controlled and decreases gradually, it could surpass the internal pressure within the plunger at some point, pushing it inward, resulting in the syringe breaking and becoming unusable. Therefore, it is crucial to use compressed air carefully in both phases of the cycle to ensure that the pressure differential between the inside and outside of the syringe is never excessive.
Practical applications of cycles with pressure support
As observed, cycles with pressure support are indispensable across various industries for processing a wide range of products. In the pharmaceutical industry, these cycles are crucial for processing pre-filled syringes, vials containing solutions, and other pharmaceuticals in liquid form packaged in containers. Without proper pressure control, these items could deform or break. Therefore, maintaining the structural integrity of these containers is essential for ensuring the sterility of the final product and its long shelf life, preventing contaminations that could have severe health implications for patients.
In the food industry, cycles with pressure support are essential for the sterilization of canned and packaged food products. These products, when subjected to high temperatures during sterilization, could undergo deformation or even rupture if the internal and external pressures are not balanced adequately. Specifically, steam-air-mix cycles cycles followed by fast cooling are widely utilized in the sterilization of products such as sauces, pâtés, and ready meals, where it is vital to preserve both the quality of the packaging and the organoleptic properties of the content.
Another significant area of application is research and clinical laboratories. Laboratory materials, such as culture media in bottles, require processing with an air over-pressure cycle to prevent volume loss due to evaporation.
In summary, cycles with pressure support provide a versatile and effective solution for a wide range of applications, enabling the sterilization of pressure-sensitive products without compromising their structural integrity or content. The selection of the appropriate cycle depends on the nature of the material to be sterilized, the type of container, and the specific requirements of each process.
Safety and efficacy considerations
The implementation of cycles with pressure support in autoclaves aims not only to enhance the efficiency of the sterilization process but also to address critical safety and quality concerns. It is imperative to ensure that the selected cycles and parameters are appropriate for the specific application. This necessitates comprehensive validation of the process for each material type and load configuration.
Safety during autoclave operation is of paramount importance. The injection of compressed air and the handling of high pressures must be meticulously managed to prevent risks such as container ruptures, explosions, or malfunctions of the equipment. Autoclave monitoring systems must be designed to detect and correct any deviations from established parameters, thereby ensuring safe and effective operation.
From an efficacy standpoint, the proper distribution of heat and pressure within the sterilization chamber is crucial to ensure that the entire load receives the necessary treatment to achieve sterility, specially in steam-air-mix cycles. Therefore, homogenization systems and/or mechanical agitation, such as radial fans, are essential for maintaining an uniform atmosphere within the chamber in applications where this cycle is employed. These systems must undergo regular maintenance to ensure their optimal functionality.
Furthermore, it is important to consider the environmental impact of cycles with pressure support as they are often accompanied by a fast cooling system. The substantial water consumption required for cooling can be significant. Therefore, optimizing these cycles to minimize resource consumption without compromising the efficacy of the process is a key consideration for sustainable operation.
In conclusion, cycles with pressure support in autoclaves represent an advanced solution for the sterilization of products sensitive to pressure and temperature, combining efficiency with safety. The correct implementation and management of these cycles require a profound understanding of the underlying physical principles, as well as a commitment to operational quality and safety.