Cycles with fast cooling
Explore how sterilization cycle with fast cooling enhances both productivity and safety in the sterilization of various load types. Gain deeper insights into this innovative sterilization technique.
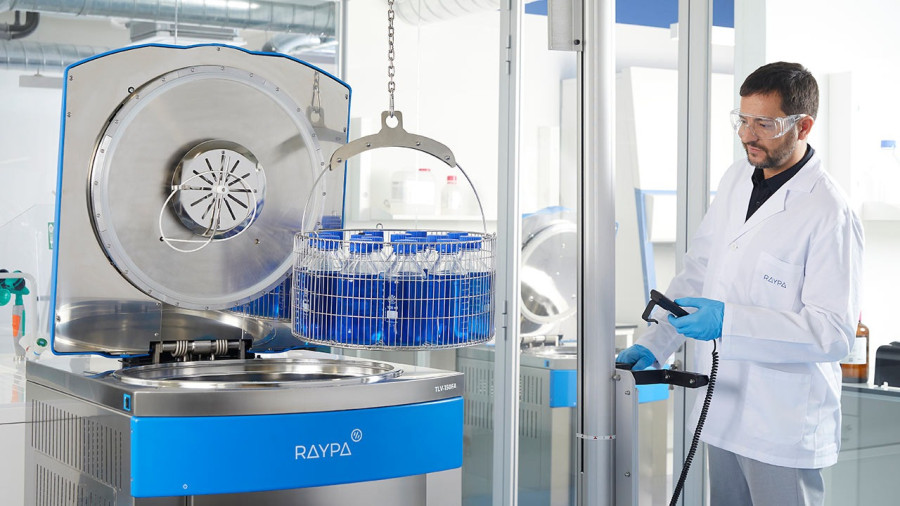
Have you considered how laboratories, research institutions, hospitals, and industrial settings might enhance their productivity in the sterilization of instruments and products via autoclaving? The key to achieving this improvement lies in the cycle with fast cooling.
In the realm of sterilization, every second counts. Efficiency and safety are paramount, and it is in this context that the cycle with fast cooling acquires crucial significance. This innovative process not only improves the operational efficiency of autoclaves but also ensures safer handling of sterilized materials.
Fundamentals of the cycle with fast cooling
The cycle with fast cooling in autoclaves represents a technological innovation designed to overcome the limitations of traditional cooling methods. This process aims to accelerate the temperature reduction of the autoclave chamber after completing the sterilization cycle.
Traditionally, cooling in an autoclave after the sterilization phase is achieved through natural heat dissipation. This passive process relies on the transfer of heat from inside the autoclave to its surroundings, a process that can be very slow and not always efficient, especially in large autoclaves or when sterilizing large volumes of liquid material. Moreover, this method may not be suitable for certain types of loads that are heat-sensitive or require rapid handling post-sterilization.
In contrast, the cycle with fast cooling employs active methods to expedite the cooling process. Among these methods are the circulation of cold water around the chamber to dissipate heat and the use of an internal radial fan. These techniques enhance the heat transfer from the sterilized items to the outside of the chamber, allowing for a faster and more controlled temperature reduction.
The most popular method is cooling through the circulation of cold water using a jacket or cooling coils that surround the autoclave chamber. By circulating cold water through these systems, heat is extracted from the chamber and the sterilized items, facilitating much quicker cooling. This method is ideal for situations where the highest speed is required but the nature of the load does not allow direct exposure to water.
Additionally, there is a method that also aims to enhance the movement of air within the chamber, utilizing fans to accelerate the cooling of the chamber. While there is an option to use external fans, those that can truly be classified as fast cooling systems are the internal fans, installed directly inside the chamber. These fans enable a faster homogenization of the chamber’s temperature.
In contrast to the previously described methods, for applications that allow direct contact of the load with water, there is the direct shower method. This is undoubtedly the fastest method but is only applicable in specific situations since the water used is not sterile. However, it is widely used in the food industry for processing hermetically sealed packaged foods. In these cases, the sterilization of interest occurs within the containers, so it is not problematic for the external surfaces to lose sterility upon contact with network water. Operationally, multiple fillings of the chamber with cold water are performed, which are then expelled to the exterior.
All these methods have specific advantages and can be selected based on the type of load, the particular needs of the sterilization process, and user preferences. Commonly, they all share the capacity to significantly improve the efficiency of the sterilization process, reducing cycle times, minimizing the heat overexposure of the load, and allowing for quicker and safer handling of sterilized materials.
Types of cycles with fast cooling
The cycle with fast cooling in autoclaves comes in two primary variants, each designed to meet specific needs and adapt to different types of loads.
Cycle with fast cooling by shower or spray
This method involves the direct injection of cold water onto the items within the autoclave chamber at the end of the sterilization cycle. The sprayed cold water rapidly absorbs heat from the items, quickly reducing their temperature. This method is suitable for processing hermetically sealed products. To prevent container breakage, this cycle must include a pressure support system using an air compressor, which injects air into the chamber effectively to counteract the sudden pressure change when cold water is introduced into the chamber after the sterilization phase. Without this pressure support, the significant temperature-induced expansion of the containers during sterilization, combined with the sudden pressure drop in the chamber, would result in container deformation and breakage.
One key advantage of this method is its ability to quickly reduce the temperature of large load volumes, making it ideal for production environments in industrial settings of the food or pharmaceutical industry. However, this system involves high water consumption, so it is common to install a water recirculation system alongside the autoclave to minimize the environmental impact of this technology.
Cycle with fast cooling by cooling coils or water jacket
In contrast to the spray method, this type of fast cooling does not involve direct water contact with the load. Instead, it uses a jacket or cooling coils surrounding the autoclave chamber through which cold water circulates. This indirect cooling method reduces the chamber temperature and, consequently, the temperature of the sterilized items, without exposing them directly to water.
This cycle is compatible with any type of load and is used for sterilizing surgical instruments or liquid loads in various settings. Additionally, this type of cooling is particularly useful for loads sensitive to sudden temperature changes.
Both cycles with fast cooling offer significant advantages over traditional cooling methods, including reduced cycle times and enhanced safety in handling sterilized items. The choice between one or the other will depend on the nature of the load, the specific needs of the sterilization process, and user preferences. By implementing these technologies, laboratories and healthcare facilities can significantly improve their operational efficiency and the safety in handling sterilized materials.
Practical applications of fast cooling in autoclaves
The cycle with fast cooling is not only a significant technological advancement; it also provides practical solutions to real-world challenges in environments where sterilization is critical. Below are the benefits of this technology in various fields:
-
Reduced wait time for reusing instruments
In hospitals and laboratories, every minute counts. Implementing cycles with fast cooling allows for quicker turnaround times for sterilized instruments. This is particularly important during peak demand periods and in workflows with high turnover of sterilized loads, enhancing operational efficiency and reducing downtime.
-
Improved food processing
In the food industry, fast cooling prevents overcooking of products. After the sterilization phase, the fast cooling by shower immediately halts the cooking process, preserving the organoleptic properties of the food. This ensures that the products are not only microbiologically safe but also appealing and of high quality for consumers.
-
Increased productivity in research centers
In microbiology laboratories where large volumes of liquid solutions are processed, time is a critical resource and often a bottleneck in the preparation of culture media. The implementation of fast cooling technology in autoclaves substantially decreases processing times, frequently saving over 60 minutes per rotation. This significant time reduction is a compelling advantage for any laboratory, as it enhances production capacity and minimizes wait times between cycles, thereby streamlining operations and boosting overall efficiency.
-
Enhanced safety in material handling
Cycles with fast cooling quickly lower the temperature of sterilized items, reducing the risk of burn injuries for operators. This procedure is particularly advantageous when processing large volumes of liquid loads, where natural cooling is very slow, and there is a significant temperature differential between the chamber and the liquid load that can be hazardous.
-
Applications in product lifecycle testing
In the medical device industry, fast cooling is essential for efficiently conducting durability tests under thermal stress conditions. The capability to heat, sterilize, and quickly cool products facilitates more productive research and quality control testing. This accelerated process significantly enhances the development and certification of new products, ensuring they meet rigorous standards in a shorter timeframe.
-
Production of culture media
Microbiologists in research centers and micropropagation technicians in biotech companies share a critical requirement: the efficient preparation and dispensing of large volumes of sterile culture media. To achieve this, specialized autoclaves with fast cooling capabilities, known as media preparators, are often used. These devices enable the swift preparation, sterilization, and cooling of substantial liquid loads to the desired dispensing temperature. This capability optimizes workflow, ensuring a continuous and reliable supply of culture media, thereby enhancing operational efficiency and productivity of the laboratory.
Further improvements in autoclaves equipped with fast cooling
The advancement of the cycle with fast cooling in autoclaves has been significantly driven by two key technologies:
-
Fan-assisted cooling
This technology involves the integration of a radial fan or an air circulation system within the autoclave chamber. The fan facilitates the uniform distribution of air towards the chamber walls, which are cooled by water coils. This active air circulation enhances the heat transfer from the sterilized items to the cold surfaces of the chamber, resulting in a faster and more uniform cooling of the load.
Fan-assisted cooling is particularly advantageous for loads that require rapid yet uniform cooling.
-
Use of flexible probes placed inside liquid samples
The sterilization of liquids presents unique challenges, particularly concerning pressure control and temperature monitoring of the load. In this context, flexible probes or core probes represent a significant innovation. These sensors are placed within liquid containers to accurately monitor the temperature of the liquid load, ensuring precise control of exposure times during the sterilization phase and temperature evolution during the cooling phase. These probes enable more accurate control, allowing the cooling system to adjust efficiently, operating only when necessary and contributing to water consumption savings.
Safety and efficacy considerations
Although advanced and efficient, in certain applications the rapid cooling cycle requires careful handling to ensure the safety and efficiency of the sterilization process:
-
Prevention of deformation, spillage, and breakage of containers
To ensure the safety and efficacy of the sterilization process, it is critical to meticulously control the temperature and pressure within both the chamber and the load during the cooling phase. This is particularly important to prevent spillage in liquid loads. When processing bottles with screw caps, it is essential to leave the caps slightly open to avoid overpressure buildup. For hermetically sealed containers, a pressure support system must be employed to mitigate the risk of rupture during processing.
-
Maintenance of product integrity and sterility
Ensuring that contaminants are not introduced during the fast cooling process is fundamental, especially in shower systems utilizing tap water. As previously noted, direct water shower systems are only suitable for sealed containers, as running water is not sterile and will contaminate any surface it contacts.
-
Preservation of autoclave integrity
Maintaining the integrity of the autoclave is crucial for ensuring its optimal functionality and prolonging its service life. A key aspect of this maintenance is the prevention of scale deposits within the chamber and on the jackets or cooling coils that are part of the cooling system. These deposits can lead to efficiency losses, blockages, or damage requiring costly repairs. To prevent such issues, it is imperative to use demineralized water to feed these fast cooling systems.
-
Environmental impact and energy efficiency
Although fast cooling systems that use water are the most effective at reducing temperature, they also entail significant water resource utilization, which can have a considerable environmental impact. However, there are various market solutions designed to mitigate this impact and promote sustainability. Notable among these are systems that combine tanks and chillers, enabling the reuse and recirculation of water at an appropriate temperature. Additionally, modern autoclaves often feature automatic water consumption control, activating and deactivating water usage as needed, thereby reducing overall water consumption.
Impact on laboratory efficiency
As discussed in this article, the implementation of cycles with fast cooling in autoclaves has demonstrated a substantial impact on the operational efficiency of laboratories. This technology not only accelerates the sterilization process but also enhances time management, resulting in increased productivity within the laboratory environment.
Reduction in cycle duration
One of the most immediate benefits of the rapid cooling cycle is the significant reduction in the overall duration of the sterilization process. By expediting the cooling phase of sterilized materials, the total time required to complete a sterilization cycle is markedly decreased. This reduction can be particularly substantial in laboratories that process a high volume of items or where a quick turnover of instruments and materials is essential. The ability to process more loads within the same time frame significantly enhances operational efficiency.
Improvement in laboratory productivity
The improved efficiency in sterilization cycles has a cascading effect on the overall productivity of the laboratory. Shorter cycles mean that sterilized equipment and materials are available for reuse much more quickly, facilitating a more agile and continuous workflow. This is particularly valuable in research environments or industries where time is a critical factor.
Furthermore, the capability to perform more sterilization cycles per day enables laboratories to handle a higher volume of work without compromising safety and quality standards. This is crucial in high-demand situations or for alleviating bottlenecks in processes.